La biomecánica revoluciona la industria española del motor: caen las lesiones y sube la productividad
El uso de realidad virtual y de sistemas de asistencia mecánicos permite reducir un 70% las lesiones y aumenta la productividad
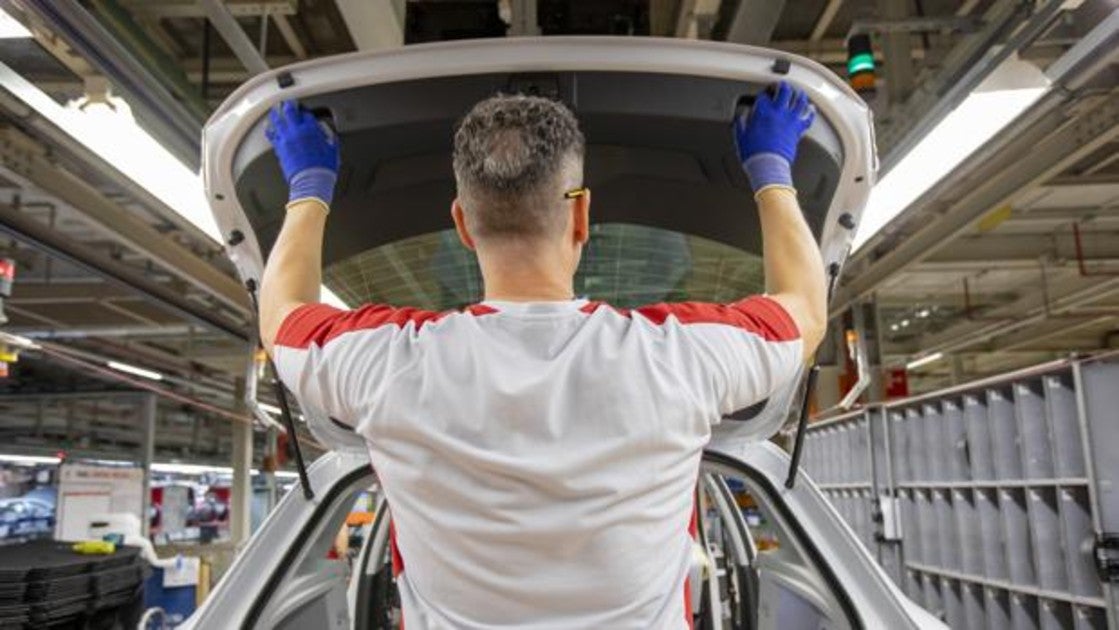
Cerca de 20 cámaras, sensores de última tecnología y gafas de realidad virtual. Podría parecer el estudio de una startup tecnológica, pero no lo es. Se trata del laboratorio de biomecánica de Seat, ubicado en el Centro de Atención y Rehabilitación Sanitaria (CARS) de Martorell.
«La tecnología nos permite recrear la línea de trabajo en nuestro laboratorio. Es necesario que el trabajador se ponga en situación y simule exactamente su tarea», explica Sonia García, responsable de Ergonomía en Seat. En el laboratorio se miden dos parámetros: el esfuerzo muscular y la posición de las articulaciones al realizar determinados movimientos. «Algunos operarios pueden llegar a realizar un mismo movimiento hasta cien veces al día. Por eso, la rotación y el diseño de la línea de trabajo son cruciales para evitar posibles lesiones», asegura.
«La biomecánica abre nuevas posibilidades de intervención en el diseño de los nuevos puesto de trabajo desde el minuto uno», explica la doctora. Patricia Such , responsable de Seguridad y Salud en el Trabajo de Seat. En funcionamiento desde 2017, se han realizado más de 4.000 estudios: «Hemos conseguido una reducción de un 70% de bajas por lesiones musculares en tan solo dos años y en el futuro queremos seguir mejorando», apunta Such. Los datos han servido, entre otros, para adaptar la línea del nuevo Seat León de manera que se rebajará 20 centímetros la altura en uno de los tramos. Una vez diseñada la línea el trabajo del laboratorio no acaba. Con la producción en marcha se siguen analizando los puestos para implementar mejoras.
Se utilizan dos tecnologías diferentes con un mismo fin. Una de ellas se basa en crear avatares en 3D. Un total de 20 cámaras combinadas con sensores capturan los movimientos de las articulaciones. Con estos datos el software de análisis construye un avatar. «Se trata de una imagen en 3D que reproduce de forma muy precisa tanto la velocidad como la amplitud del movimiento. Es una tecnología equivalente a la utilizada para crear los personajes de un videojuego, pero con un nivel de precisión mucho más alto», explica Sonia García.
La otra tecnología es la realidad virtual. La gran ventaja de este sistema es que permite anticiparse y realizar cambios antes de que la línea esté en funcionamiento. « Podemos simular diferentes posiciones hasta encontrar la mejor opción , por ejemplo, para la colocación del portón del maletero. Esto nos permite ganar tiempo y supone un coste menor que realizar las pruebas en la línea real», destaca García.
Inspiración deportiva en Ford Almussafes
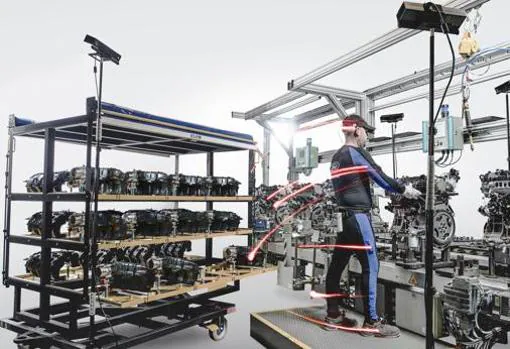
De forma paralela, los empleados de la planta de Motores de Ford en Almussafes (Valencia) están usando un traje especial equipado con tecnología avanzada de seguimiento corporal . El sistema piloto, creado por Ford y el Instituto Biomecánica de Valencia, ha involucrado a 70 empleados en 21 áreas de trabajo .
La tecnología de movimiento de los jugadores suele registrar cómo corren o se mueven los atletas, lo que permite a los entrenadores deportivos y a los desarrolladores de juegos mejorar el potencial de las estrellas del deporte en el mundo real o en la pantalla. Ford lo está usando para diseñar estaciones de trabajo menos estresantes físicamente para mejorar la calidad de fabricación.
«Se ha demostrado en el campo de deportes que, con la tecnología de seguimiento de movimiento, los pequeños ajustes en la forma en que te mueves pueden tener un gran beneficio», explica Javier Gisbert, gerente de área de producción de la planta de Motores de Ford en Valencia. «Para nuestros empleados, los cambios realizados en las áreas de trabajo que utilizan tecnología similar pueden garantizar en última instancia que, incluso en un día largo, puedan trabajar cómodamente ».
Los ingenieros se inspiraron en un traje que vieron en un evento que demostró cómo los robots podían replicar el movimiento humano y luego aplicarlo en su lugar de trabajo, donde este mes comenzó la producción de la nueva Ford Transit Connect y los motores EcoBoost Duratec de 2.0 litros.
El ajustado traje cuenta con 15 pequeños sensores de seguimiento de movimiento conectados a una unidad de detección inalámbrica. El sistema realiza un seguimiento de la forma en que la persona se mueve en el trabajo, destacando los movimientos de la cabeza, el cuello, los hombros y las extremidades. El movimiento es grabado por cuatro cámaras especializadas en seguimiento del movimiento, similares a las que se utilizan normalmente en las consolas de videojuegos, situadas cerca del trabajador y capturadas como una animación en 3D del usuario.
Los ergónomos especialmente formados utilizan los datos para ayudar a los empleados a alinear su postura correctamente. Las mediciones capturadas por el sistema, como la altura o la longitud del brazo de un empleado, se utilizan para diseñar estaciones de trabajo , de modo que se adapten mejor a los empleados.