INDUSTRIA
Así se fabrican los 'huesos' de un avión
La empresa gaditana Mecanizados y Montajes despunta en el sector aeronáutico como proveedor de piezas y componentes en chapa
Dos exejecutivos de Airbus logran poner en órbita esta pyme aeronáutica que ofrece un catálogo con más de 4.200 tipos de piezas para programas de Airbus, Boeing y Embraer
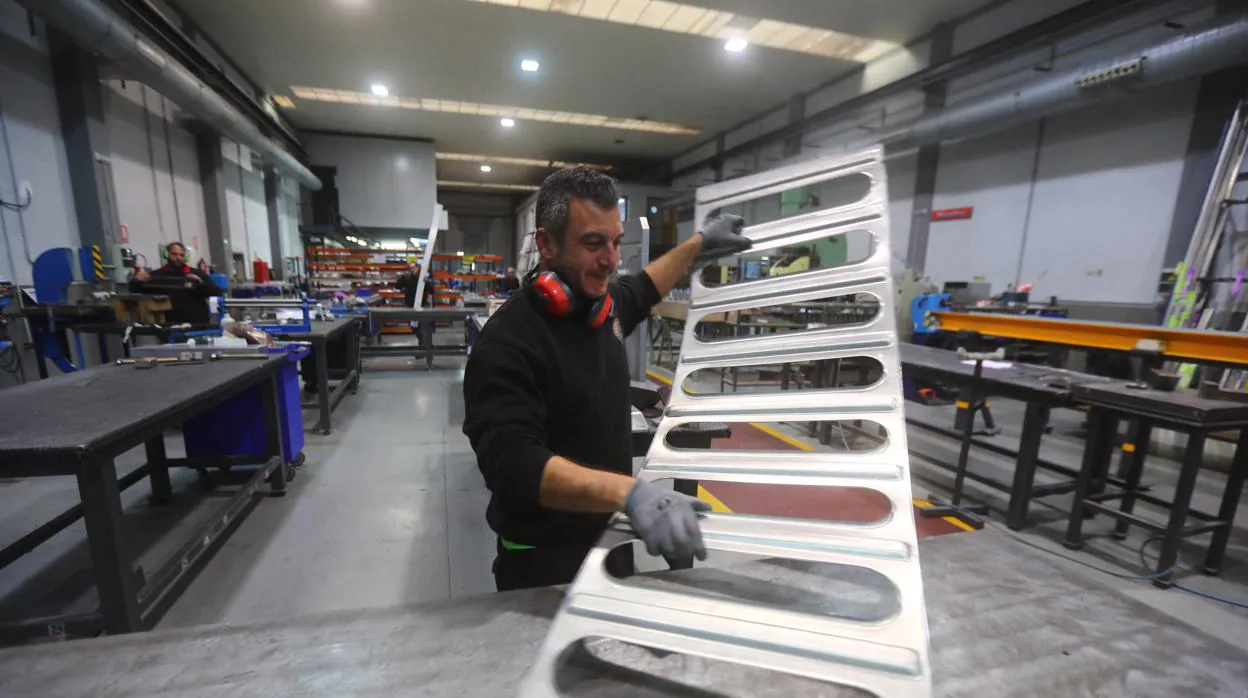
No hay margen para el error ni tampoco para la improvisación. Todo tiene que estar milimétricamente medido y ajustado. Cualquier fallo puede acabar en tragedia. La fabricación de las piezas que integran la estructura de un avión forma parte de un complejo sistema que obliga a una verificación permanente de la cadena de producción . La empresa gaditana Mecanizados y Montajes (M&M) elabora muchos de los componentes que se encuentran en el aparato y que cuando subimos a bordo, pese a su importancia, pasan inadvertidos.
Esta compañía es una de las proveedoras de las grandes empresas tractoras de la aeronáutica y tiene como especial relevancia su especialización en la fabricación de piezas de acero, aluminio y titanio . Mecanizados cuenta con tres plantas en la provincia (dos en El Puerto y una en la localidad serrana de Espera) y el interior de cada una de ellas guarda cierto parecido con un anatómico forense de la aviación . De sus naves salen perfiles y estructuras, tanto curvas como planas, para distintas secciones del avión. El catálogo de este proveedor industrial ofrece una variedad de entre 4.200 y 4.400 piezas .
Mecanizados y Montajes es uno de los ejemplos de la industria auxiliar aeronáutica de la Bahía que despliega sus alas como proveedor Tier 2 de Airbus, Boeing, Embraer y abastece también a los proveedores de primer nivel (Tier 1) como Alestis, Aernnova y Aciturri. Una mediana empresa de gran calado. LA VOZ ha girado una visita a las tres plantas de la compañía precisamente en la misma semana en que el gigante Airbus anunciaba el fin de la producción del A380 para el año 2021 . Se trata de un avión emblemático para la Bahía de Cádiz ya que entre 2003 y 2004 la planta de Airbus de Puerto Real se acondicionó para albergar la construcción de su timón de cola, el estabilizador y parte de la panza o 'belly fairing'. El A380 realizó en abril de 2005 su primer vuelo de pruebas y el avión surcó entonces el cielo de Cádiz. En 2006 arrancó su comercialización y fue cuando la industria auxiliar gaditana se hizo con la subcontratación de piezas de este superjumbo. La decisión de Airbus de cancelar este programa aeronáutico conlleva ahora a la industria auxiliar a tomar medidas y orientar sus acciones hacia otros programas y otras compañías.
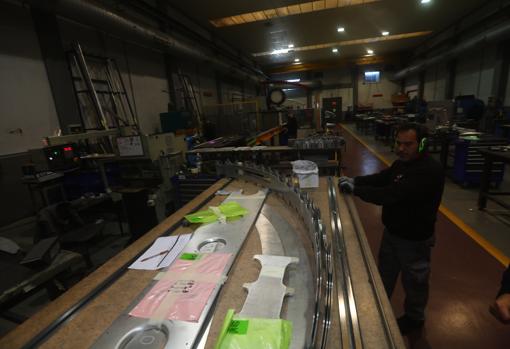
El tejido aeronáutico que se ha desarrollado en la Bahía al amparo de Airbus es amplio y variado. En 2016, la Junta de Andalucía elaboró un informe sobre la pujanza del sector aeronáutico en el espacio Cádiz-Sevilla. La provincia cuenta con tres compañías proveedoras de primer nivel . Este tipo de suministradores se caracteriza por tener suficiente capacidad industrial, técnica y financiera para captar grandes contratos de los principales constructores aeroespaciales mundiales sin necesidad de intermediarios. Estas empresas son Alestis Aerospace, Aernnova Andalucía y Aerosur (Grupo Aciturri) . Actualmente en el sector aeronáutico de Cádiz se han identificado 41 empresas que pertenecen a la industria auxiliar o trabajan como subcontratistas tanto para empresas tractoras como para otras auxiliares.
Proceso de alta calidad
Respecto a la ubicación, destaca El Puerto como ciudad que alberga el mayor número de empresas auxiliares con 13 de ellas (32%), seguido de la capital con 11 (27%) y Puerto Real con ocho (20%). Estas empresas se centran sobre todo en los servicios especializados de ingeniería aeronáutica o actividades de montaje de medianos y pequeños conjuntos. Además, el 58% de las empresas han sido creadas para cubrir las necesidades del sector y únicamente el 16% provienen de la Universidad (spin off). La industria aeronáutica andaluza en general, así como la provincial, ha ampliado en los últimos años su facturación , capacidad de producción, plantillas e inversiones en formación y adaptación a la normas de calidad e I+D, reforzando el sector con proyectos de concentración empresarial y diversificando productos y clientes.
En lo que respecta al empleo, el estudio refleja que las empresas de Cádiz aglutinan el 22% del empleo directo del sector en Andalucía, y suma un total de 2.599 puestos de trabajo entorno al sector en la provincia. Por otro lado, el eje Sevilla-Cádiz protagoniza casi el 100% de las exportaciones del sector.
La empresa Mecanizados y Montajes logró el año pasado fabricar 800.000 piezas . Su director general, Javier Pizarro, un histórico exejecutivo de Airbus, destaca que las tres plantas de la empresa están al 65% de su capacidad, es decir, hay margen todavía para aumentar la producción. El proceso de fabricación resulta complejo y muy distinto al que se sigue, por ejemplo, en el sector de la automoción . La aeronáutica no trabaja en serie sino a través de procesos mecanizados donde cada elemento tiene una especie de vida propia. No hay que olvidar que la pieza final, por pequeña que sea, sale de fábrica con una grabación impresa a modo de código que recopila todos los datos de su origen y montaje
Mecanizados y Montaje cuenta con una plantilla de 180 trabajadores. Cada una de las tres plantas de esta firma gaditana tiene una función específica. Mientras que la del polígono de Las Salinas, en El Puerto, se encarga del conformado y tratamiento de componentes, la segunda factoría, situada en el polígono portuense de Tecnobahía, prepara diseño y utillajes o moldes. La de Espera está especializada en la fabricación de perfiles con tratamientos térmicos. Pizarro destaca que la empresa participa en los programas aeronáuticos del A380, A350, A330, A320neo, A400M, MRTT y C295 de Airbus. También en el B787 y B737 MAX de Boeing, además del KC390 de Embraer.
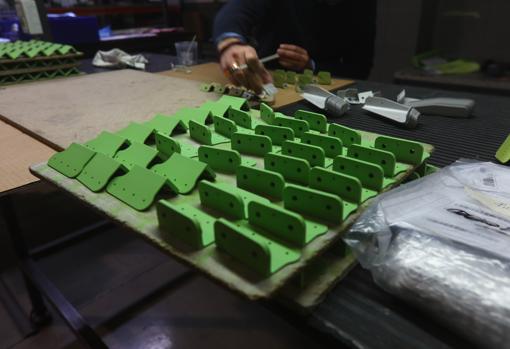
El proceso de fabricación de una de estas piezas forma parte de una cadena de producción de alta calidad en la que se certifica y verifica de principio a fin todo el viaje del componente , es decir, desde que es un embrión en las bobinas metálicas hasta su corte y posterior paso por el utillaje para adquirir la forma. Cada pieza en cuestión cuenta con una hoja de ruta anexa en la que los operarios de las distintas secciones que intervienen en la cadena de fabricación anotan y especifican los pasos del proceso. Asimismo, otra de las actuaciones que resulta inquietante en el desarrollo de estos componentes aeronáuticos es su verificación de calidad. Una vez terminadas, las piezas pasan por un detector de impurezas . Una cámara oscura con luces especiales permite al ojo humano detectar grietas en las superficie. Si alguno de los componentes recibe el visto bueno con defectos el problema se traslada a la cadena de montaje de la estructura del avión.
De un taller a tres factorías
Esta empresa, que resume fielmente el proceso de fabricación que desarrolla un proveedor aeronáutico, nació en 2004 de la mano del empresario Juan Ferreras, natural de Espera. Se trata de un iluminado que vio en el negocio de la chapa la diversificación hacia la aeronáutica. La empresa nació como un pequeño taller para dar servicio a la planta de Airbus del Puerto de Santa María (CBC) . En una década forjó una factoría especializada en la fabricación de perfiles aeronáuticos complejos, chapistería utillaje y recanteado. La irrupción de la fibra de carbono en la última década ha llevado al común de los mortales a creer que los aviones más modernos están fabricados en ‘composite’, pero buena parte de la estructura de los aviones se hace en chapa y acero. La empresa de Ferreras se enfrentó a una dura crisis financiera a los diez años de su fundación y fue entonces cuando el empresario lanzó un SOS.
Así, Domingo Ureña, expresidente de Airbus España, entró como socio de la empresa con el ánimo de evitar el concurso de acreedores . Ureña lanzó un plan de viabilidad para doblar ingresos en 2020, hasta los 22 millones, y superar el crítico año 2015. Ureña desembarcó en M&M cuando la empresa contaba una deuda de 3 millones de euros, en su gran mayoría contraída con las administraciones públicas. La inyección de liquidez de Ureña permitió en cierto modo ponerse al día de los pagos y iniciar un plan de reestructuración de ese pasivo.
El expresidente del grupo Airbus en España entre 2009 y 2015 ha mostrado siempre su confianza en el modelo de negocio de M&M
La empresa facturó 11 millones en 2015 y nunca ha dejado de dar beneficio. Sin embargo, las dificultades para financiar el funcionamiento diario, la reducción o bache en algunos de sus programas clave como el A380 o el A400M, y el parón sufrido en la planta de Airbus en El Puerto (CBC) lo situaron a cierre de 2015 en una situación muy delicada.
El plan de Ureña simplificó societariamente M&M creando una sola sociedad. Recortó costes, reestructuró la empresa, además de implantar un plan de diversificación geográfica para captar nuevo negocio.
En junio de 2016, el propio Ureña fichó para Montajes y Mecanizados a Luis Pizarro, un ejecutivo histórico de Airbus España, que salió de esta compañía a finales de 2015 . Pizarro es nombrado director general de M&M en sustitución de a Mamen Vergeles. Pizarro cuenta con más de tres décadas de experiencia de gestión en el sector aeronáutico, siempre en la órbita del grupo Airbus, donde ha ocupado diversos puestos de responsabilidad, entre ellos, la dirección de Airbus Operaciones. Fue también subdirector de Montajes y Entregas en Puerto Real y director de las fábricas de Illescas, en Toledo, y Getafe, en Madrid.
En octubre de 2017, Ureña traza una nueva hoja de ruta para convertir la empresa en uno de los mayores proveedores aeronáuticos andaluces. La meta es doblar su negocio en un plazo de tres años y alcanzar así unas ventas de 20 millones . El crecimiento en el ritmo de fabricación de las aeronaves en las que está presente y la búsqueda de nuevos clientes fuera de España son la base para su expansión. Tras negociar con el Ministerio de Industria, la Seguridad Social y Hacienda la deuda se ha logrado que una parte muy importante de los compromisos de pago sean a largo plazo, lo que ha dado oxígeno a la caja de la compañía y fiabilidad a los bancos.
En 2018 llevó a cabo un ambicioso plan de transformación el sistema de gestión interno de la compañía, gracias a un crédito del Ministerio de Industria. La compañía ha superado las turbulencias y afronta el futuro con optimismo.