INDUSTRIA
La fábrica más eficiente del mundo está en Andalucía
Atlantic Copper es la refinería que encabeza el ránking global de menor consumo de energía unitario gracias a unas inversiones cercanas a 200 millones
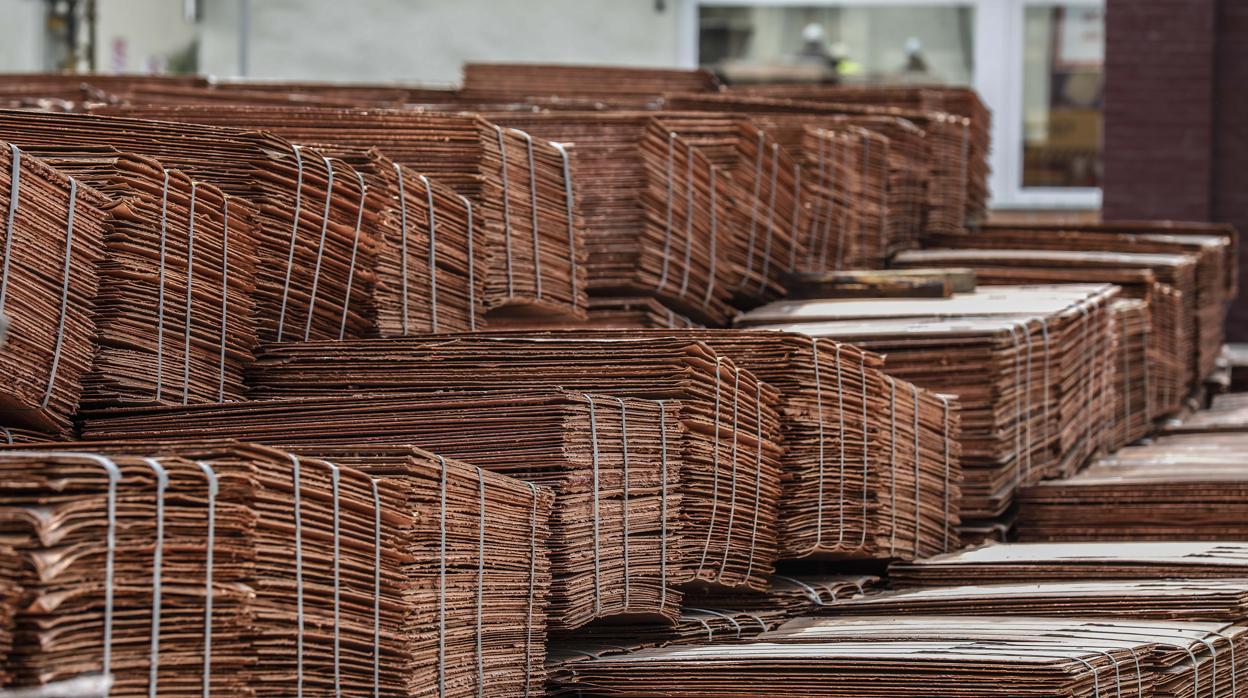
En la explanada que preside la entrada de Atlantic Copper , un gran complejo industrial de cincuenta hectáreas frente a las marismas del río Odiel, reposan miles de planchas de cobre de alta calidad (denominadas cátodos) , que esperan su turno para viajar rumbo a países de Asia y el resto del Mediterráneo (la firma exporta casi el 50% de su producción). La imagen del metal rojo saliendo en camiones hacia el Puerto representa el final de un largo proceso que comienza con la compra de mineral concentrado de cobre a minas de todo el mundo, su clasificación, fundición y refino.
La planta onubense, que genera 3.000 empleos , es única en España y la tercera en dimensión del Viejo Continente, aunque el dato más relevante está en el ránking mundial en eficiencia energética que elabora Wood Mackenzie , donde ocupa la primera posición.
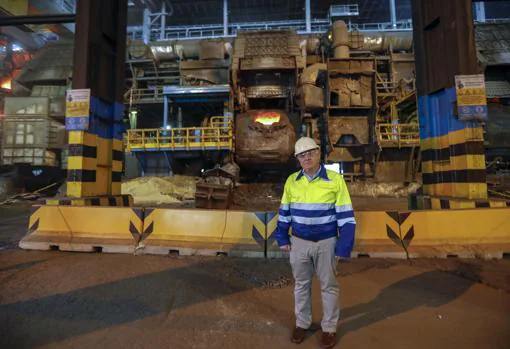
Las medidas de ahorro y sostenibilidad son vitales para la consolidación y supervivencia de la industria pesada en un mercado tan maduro como Europa, y el gran ejemplo de que Andalucía puede abanderar este movimiento se encuentra en esta factoría de Huelva. «El precio internacional del cobre lo determina el mercado, nuestra obligación es que el proceso de fabricación sea excelente para competir con rentabilidad a escala global», afirma Miguel Palacios, director general de Metalurgia de Atlantic Copper.
«El gran consumo de energía está relacionado con todo lo que rodea al movimiento de gases en este proceso» , remarca Palacios, que pone un ejemplo: «El horno de la fundición produce gases con dióxido de azufre, se enfrían en una caldera y generamos vapor con el que movemos turbinas, que producen la energía eléctrica que reaprovechamos de nuevo en la refinería».
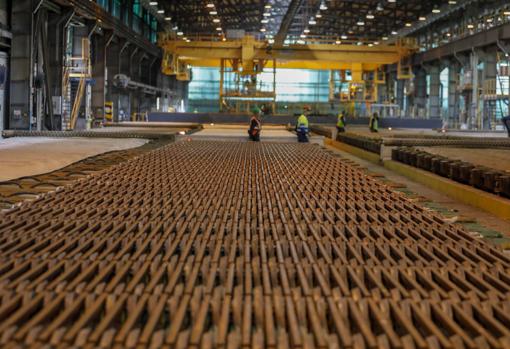
Este proceso —unido a otras múltiples tecnologías desarrolladas en el seno de la factoría— facilita que la compañía genere por sí misma el 25% de sus necesidades. El otro pilar está en la mejora de su eficiencia operativa. Con la misma capacidad productiva, Atlantic Copper funde más de 1,1 millones de toneladas de concentrado de cobre al año, frente a los 950.000 de hace una década. La clave ha sido «reducir drásticamente las paradas por fallos en la planta con un mantenimiento preventivo y predictivo , con lo cual se eleva la disponibilidad y se produce más horas durante el año».
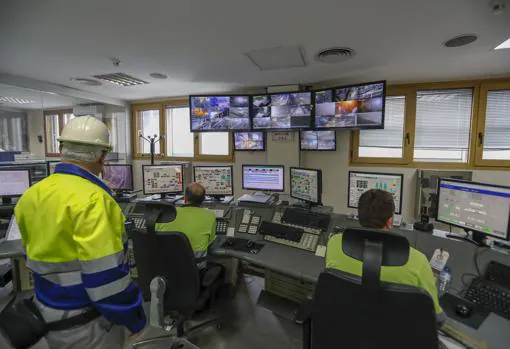
Otro de los factores que han determinado claramente la evolución de la compañía ha sido su cercanía a un gran núcleo de población como es Huelva. Miguel Palacios subraya que «se ha reducido la emisión de partículas casi un 80% en diez años y las emisiones de dióxido de azufre han caído un 26%, lo que nos convierte en una instalación limpia y plenamente respetuosa con el entorno».
La planta recicla la mayor parte del agua que utiliza y se plantea como objetivo a medio plazo reutilizar el 100% (el consumo de agua cayó un 11% en 2017). En los últimos cinco años ha invertido más de 150 millones y hasta 2020 desembolsará otros 80 millones. Y_la próxima frontera de Atlantic Copper serán las energías renovables con las que espera cubrir más del 25% de sus necesidades.